Powder Power – How Brompton Bikes are Painted
For many years now, Brompton bikes have come in a vibrant array of colours. From standard to premium finishes, mix and match extremities, and a myriad of special edition bikes released each year, you may wonder how they get that consistent great finish. We visited the factory in Greenford to find out how they do it.
Brompton began full-time production of their one-of-a-kind bikes under some railway arches in Bollo Lane, Brentford, in 1988. As demand grew, the team moved into a larger, 22,000 square-foot factory in nearby Lionel Road South, near Kew Bridge station. In these early phases, there simply wasn’t space to do in-house painting, so the bike frames were loaded onto a truck and driven to a specialised paint facility over 325 km away in Wales. Not terribly environmentally friendly!
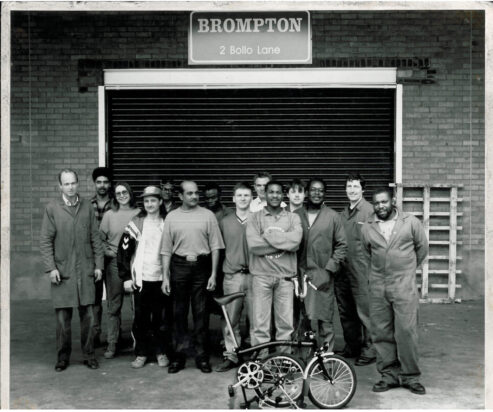
In 2016, Brompton outgrew their old digs, moving its factory from Brentford to an 84,000-square-foot facility in Greenford, West London. They transformed a simple warehouse into a state-of-the-art factory. The new facility allowed Brompton to boost production to around 100,000 folding bikes annually, meeting growing global demand while keeping their skilled workforce of over 300 employees.
The relocation and expansion also meant that they could bring the painting in-house, saving time, fuel, and money. Brompton invested over £1,000,000 on a first-class powder-coating machine. Powder coating offers a thick, durable, and long-lasting finish. Coupled with the pretreatment process, this improves longevity and gives that famous fine Brompton finish.
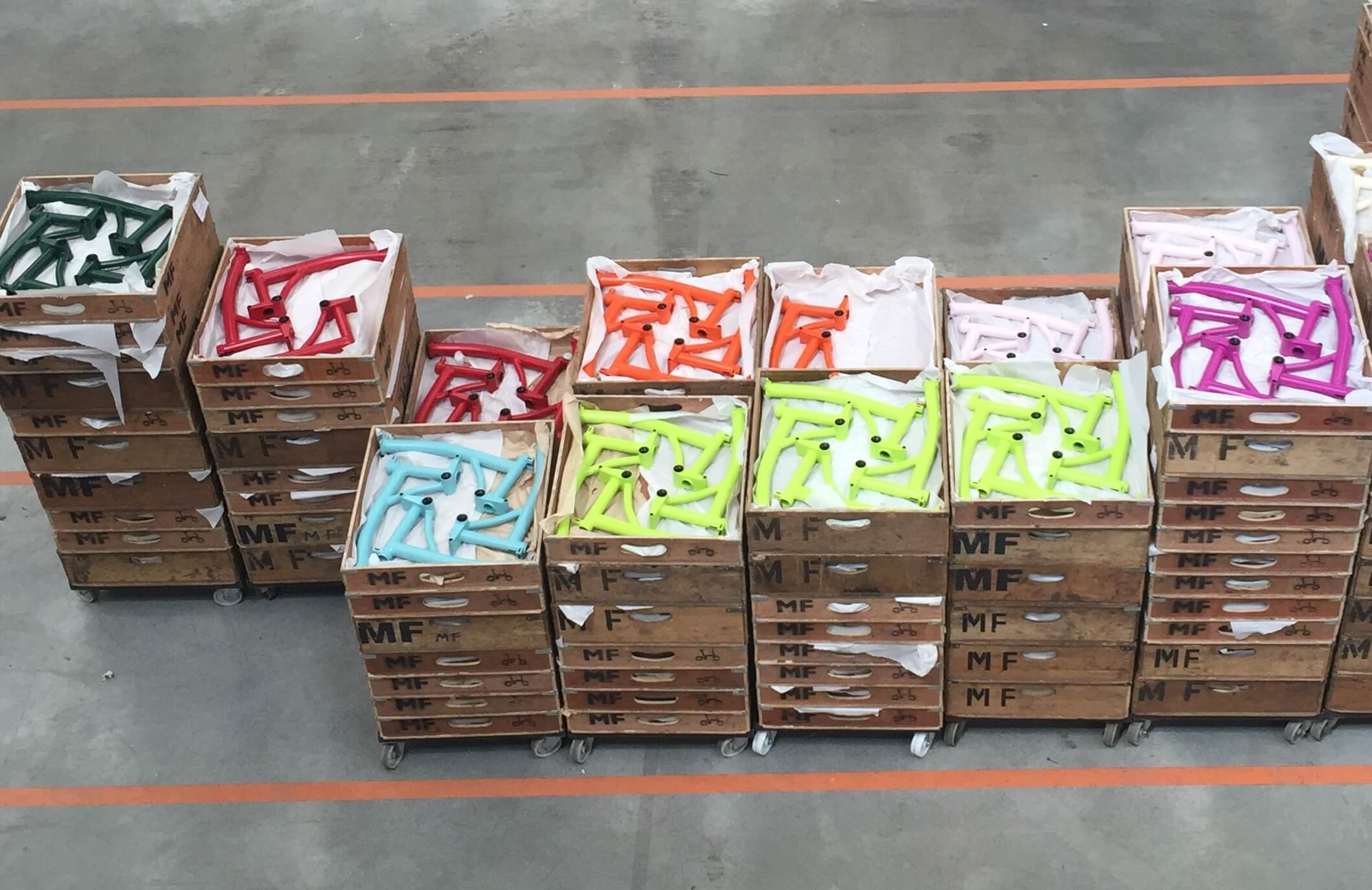
Here’s how it works:
First, the frame components are pretreated. This process is crucial for preventing corrosion on the steel. Brompton employs an eco-friendly Chemetall Oxsilan process, which ensures high corrosion resistance and paint adhesion while meeting strict environmental standards. The pretreatment plant features high-efficiency gas burners, stainless steel construction, and advanced water treatment.
After pretreatment, components dry in a gas-fired oven at 302 degrees for seven minutes. They then move to a pressurized, ventilated enclosure to prevent contamination. An automatic powder coating booth sprays a plastic powder onto the frame part using an electrostatic charge. Manual touch-ups ensure complete coverage. The components cure in an oven at 392 degrees for 25 minutes before cooling and undergoing rigorous inspection. Only perfect parts make the cut; anything less is recycled.
- Want to see the painting process in action? Check out Brompton’s video of the Nine Streets Edition.
- Come visit our store in Toronto to see the full colour lineup in person!
- See all Past Colour Guides and Associated RAL Codes
- Brompton 2023 Seasonal Colour – Bumblebee Yellow
- Brompton 2023 Seasonal Colour – Emerald Green Lacquer
- Brompton 2024 Seasonal Colour – Pop Lilac